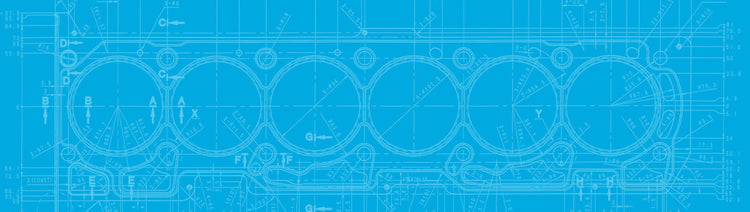
Shaft Finish, Hardness and Tolerance
If a radial lip oil seal is to perform correctly, the condition of the shaft surface where the seal is to operate, is as important as the condition of the seal itself. Shafts having too rough or too smooth a finish, will greatly affect the performance and service life of the seal. Research by oil seal manufacturers recommend that the shaft surface at the point of seal lip contact, be machine lead free with a finish between 0.25 micrometres to 0.50 micrometres Ra (10 microinches to 20 microinches).
The preferred method of achieving this finish is by plunge grinding, to spark out with short to medium marks which are at 90 degrees to the shaft axis. These machine marks retain oil which improves seal life. A grinding wheel of 80 grits is recommended. The ratio grinding wheel rpm. to the shaft rpm. must not be a whole number ratio or lead will result (i.e. 10.5 : 1 not 10 : 1). To assist in installation of the oil seal, the leading edge of the shaft should be chamfered 15/30° with the corners blended and burr free.
Another shaft condition relevant to oil seal performance is hardness. Oil seal manufactures recommend a minimum shaft hardness of 45 Rockwell C to prevent excessive wear.
Oil seals are designed and manufactured to operate on a specific shaft diameter. For shafts up to 100mm (4.0”) in diameter the tolerance is ±0.08mm (0.003”). Shafts 100 to 150mm (4.0 to 6.0”) in diameter the tolerance is ±0.10mm (0.004”).
Housing
A bore chamfer is necessary to assist in the installation of the oil seal. A proper chamfer angle 15/30° and depth of 1.5~2.5mm minimizes cocking or lack of squareness of the seal to the shaft, distortion of the seal case and reduces force required in assembly.
![]() |
![]() |
For metal case seals a bore surface finish of 0.25 micrometres Ra (100 microinches) is recommended. A slightly rougher surface finish of 0.375 micrometres Ra (150 microinches) is acceptable for rubber case seals. Excessively rough bore finishes may allow paths for fluid to leak between the seal OD and the bore. Too smooth a finish may allow the seal to back out of the bore.
Installation
Before the installation of any oil seal, it should be checked that no foreign matter is adhering to the seal, that the sealing lip is not damaged, cut or distorted and the garter spring has not been displaced. The sealing lip of the oil seal should be pre-lubricated to reduce friction on the contact surfaces and help protect the seal lip during initial run-in. The case of the oil seal should be dry and free of dirt. Do not lubricate or apply any retaining agent to the seal case.
An installation tool should always be used when installing an oil seal. The use of a tool improves ease of installation and reduces the possibility of seal cocking (non-perpendicular to shaft). A hydraulic or pneumatic press is advised to supply the necessary, uniform force to install the seal.
The advisable sequence for oil seal installation is to install the seal over the shaft and then in the housing bore. Care should be taken not to damage or deform the seal lip. When installing over a keyway or spline, a sleeve or bullet should be used to protect the seal lip from cuts or tears. Where the shaft must be installed through, the seal centering guides for the shaft will prevent lip deformation and dislodging of the spring. When possible, the shaft should be rotated as it passes through the seal to reduce sliding friction.